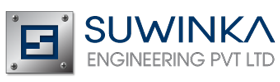
Suwinka engineering can open native solid works, autocad and fabriwin . Our engineers are fluent with each of these software programs and we own many sets of these softwares. Suwinka engineering can engineer your projects from your ideas or help you in your design process.
Suwinka engineering has the following software in-house to simplify our process for sheetmetal punching and bending.
♦ Fabriwin
♦ Autocad
♦ Solidworks.
Our CNC punches are state of the art. Improvements in press drive technology, machine control design, tooling, and CAD/CAM programming software are increasing the throughput capability and the overall versatility of CNC turret punch press equipment in our shop.
CNC punches have high hit rates on the mechanical ram system as a direct result of the faster axis speeds and quicker acceleration and deceleration supplied by servo systems. A mechanical ram has a fixed stroke length, which starts at the fully retracted position and finishes with the ram at the exact bottom position.
Specifications:
♦ Sheet size capacity : 1270mmx2540mm
♦ Sheet thickness : max. 3mm Mild steel / 3mm stainless steel / 4mm Aluminium
♦ Punching accuracy : +- 0.07mm
♦ Turret station : 31
♦ Press capacity : 22 ton
A press brake is a press used to bend, form or punch metal. It is a press that exerts a force on a set of dies. The force can be created by mechanical, hydraulic, electric or manual means.
More complicated parts require interface with a CNC back gauge to allow the operator to more accurately position metal for forming. Our state-of-the-art precision press brakes are of a unique up-acting design in which the hydraulic cylinders in the lower beam match the deflection of the upper beam to eliminate part canoeing and deliver consistent production quality.
Our high tonnage press brakes offer a wide range of capacities for various materials.
Specifications :
♦ Bending capacity : up to 4mm steel
♦ Between frames : 2500mm
Metal inert gas welding(MIG)
It is a semi-automatic or automatic process that uses a continuous wire feed as an electrode and an inert or semi-inert gas mixture to protect the weld from contamination. Since the electrode is continuous, welding speeds are greater for GMAW than for SMAW. The equipment required to perform the GMAW process is more complex and expensive than that required for SMAW, and requires a more complex setup procedure. GMAW is well suited to production welding. The process can be applied to a wide variety of metals, both ferrous and non-ferrous.
¤ Shielded Metal Arc Welding (SMAW) -
Also known as stick welding. Electric current is used to strike an arc between the base material and consumable electrode rod, which is made of steel and is covered with a flux that protects the weld area from oxidation and contamination by producing CO 2 gas during the welding process. The process is generally limited to welding ferrous materials.
¤ Spot Welding -
A resistance welding method used to join overlapping metal sheets of up to 3 mm thick. Two electrodes are simultaneously used to clamp the metal sheets together and to pass current through the sheets. The advantages of the method include efficient energy use, limited work piece deformation, and no required filler materials. Weld strength is significantly lower than with other welding methods, making the process suitable for only certain applications on ferrous metals.
¤ Oxy-acetylene Welding -
The flame is applied to the base metal and held until a small puddle of molten metal is formed. The puddle is moved along the path where the weld bead is desired. Usually, more metal is added to the puddle as it is moved along by means of dipping metal from a welding rod or filler rod into the molten metal puddle. The metal puddle will travel towards where the metal is the hottest. This is accomplished through torch manipulation by the welder.
Stud welding -
Stud welding is a form of spot welding where a bolt or specially formed nut is welded onto another metal part. The bolts may be automatically fed into the spot welder. Weld nuts generally have a flange with small nubs that melt to form the weld. Studs have a necked down, un-threaded area for the same purpose.
To provide Suwinka customers with scratch and burr-free parts, we utilize state-of-the-art Hitachi graining/deburring machines and an extensive array of tumbling and grinding equipment. Our highly skilled finishers can handle all of your finishing needs.
¤ Pre-treatment - We have 11 tanks Automatic pre-treatment process with hot air Drier. Material should pass through Pre-treatment process before powder coating. Dust particles, oil , welding scales, metal oxide and rust on surface of metal gets removed in pre-treatment process and Thin layer of Phosphate gets form on surface which prevent metal for getting Rusty in Future and improves bonding of powder with metal.
¤ Powder Coating - Powder coating is a type of coating that is applied as a free-flowing dry powder. The main difference between a conventional liquid paint and a powder coating is that the powder coating does not require a solvent to keep the binder and filler parts in a liquid suspension form. The coating is typically applied Electrostatically and is then cured under heat to allow it to flow and form a skin. We can accommodate parts up to 1400mm deep, 2500mm long and 600mm wide. The quality is checked continuously with a paint thickness, scratch and cure test. The skilled painters are also able to provide perfect finishes by hand on intricate work. We stock a wide range of colours and finishes including satin, gloss, matt, leatherette, texture and plasticoat finish. Our powder coating has pass through 1000hrs salt spray test as per ASTM B113.
± Contact Person - Mr. Manoj Deore.
± Address - R-971 MIDC Rabale Navi Mumbai - 400701
± Call Us - +91-9820462615
Landline No - 022-27692812/13/14
± E-mail id - suwinka98@gmail.com
Copyright © 2015. Suwinka Engineering Pvt Ltd. All Rights are Reserved. Developed and Managed by SME Business Services Ltd.