Rotary Vacuum Paddle Dryers
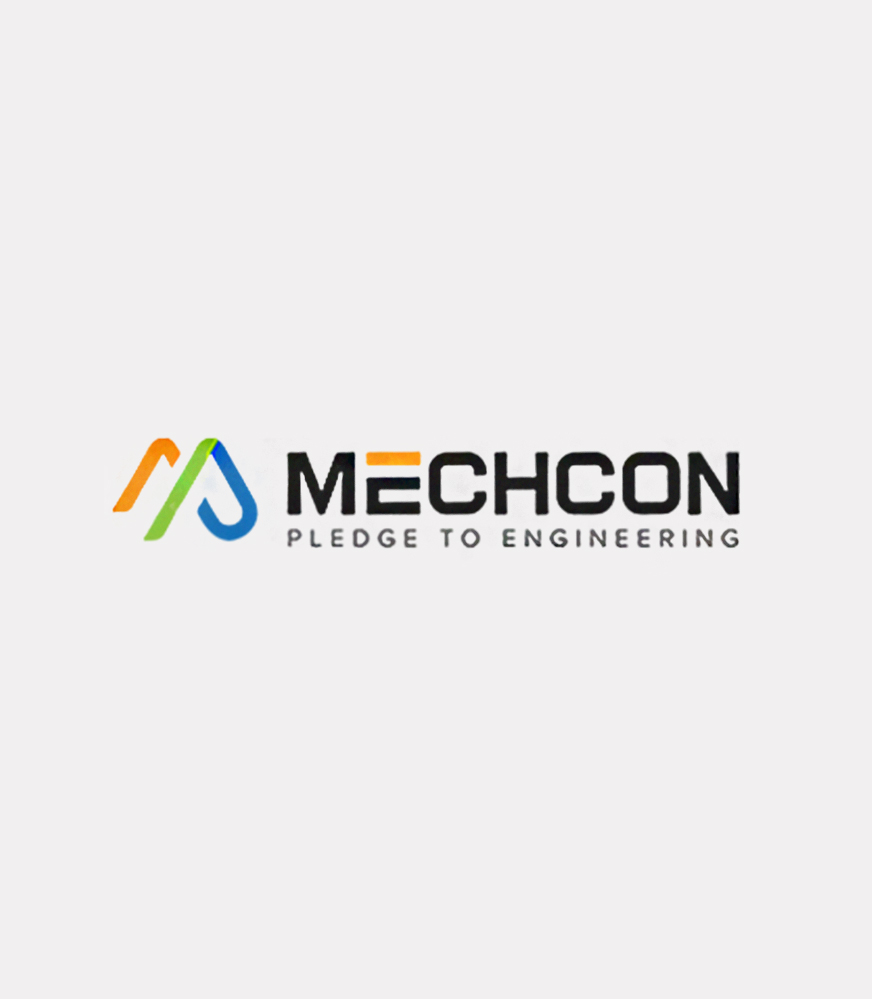
Rotary Vacuum Paddle Dryers
Many powdered solid products require dehydration and solvent recovery from wet cake and slurries. Rotary Vacuum Paddle Dryers (RVPD) are a perfect solution to overcome these issues. These RVPDs are specially designed to dry products that are temperature sensitive, are susceptible to oxidation, volatile, and those that are toxic in nature ACME RVPDs are great substitutes to other types of dryers that cause air-contamination. ACME provides turnkey solutions covering design to fabrication, installation and commissioning of the entire RVPD plant.
RVPD is the most versatile dryer which can handle the products having lumping properties. The integrated drying, mixing and breaking process in single unit under vacuum provides enhanced drying efficiency with low LOD values at low working temperatures, and process economy due to high solvent recovery. It can be used for low temperature drying, extraction of useful solvents, reaction, crystallization, and recovery of solvent. RVPD consists of jacketed shell with a central agitator shaft having paddle/blades which rotates at a very low RPM. The low clearance agitator paddles/blades scrape the material against the internal heated surface of shell, which provides maximum heating consistently. For uniform drying of product, heat transfer fluids such as hot water or steam is circulated through the shell jacket. This completely jacketed system provides optimum dryer efficiency.
Features
- cGMP-compliant equipment design & construction
- Short drying time
- Efficient design of paddle agitator
- Gives uniform size and homogeneous dried product
- Eliminates product handling and product exposure which ensures maximum operator & environmental safety
- Uniform contact between the material, and combined heat from the surface of the dryer and paddle agitator shaft
- Dried product contains very low final moisture content
- Ease of internal cleaning, operation, inspection and validation which eliminates the chances of product contamination
- High vacuum augments the integrated heated system to enable low temperature drying
- Operating cost reduction due to low energy consumption
- High heat transfer efficiency
- Maximum solvent recovery
- Eliminates degradation of product since there isn’t over-exposure, higher temperature and drying time
- Pulsating filter facilitates dust free operation