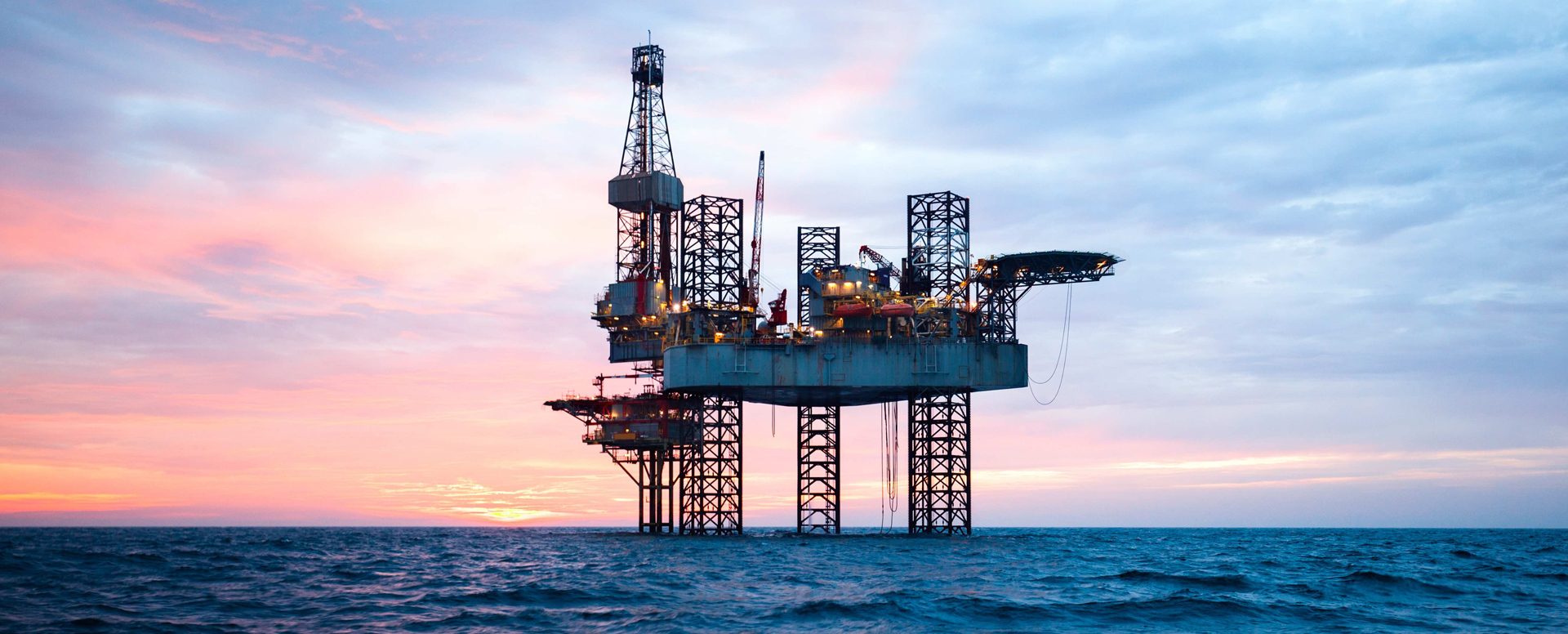
Engineering Plastics: Weathering the Storms in Offshore Applications
The offshore industry operates in a demanding environment, facing constant challenges from saltwater, harsh weather, and heavy loads. Engineering plastics are proving their mettle in this sector due to their properties that withstand these rigorous conditions:
Corrosion Resistance:
Unlike metals, many engineering plastics are naturally resistant to saltwater corrosion, eliminating the need for expensive coatings and extending the lifespan of offshore equipment.
Flame Retardant Options:
Some engineering plastics are formulated with flame retardant properties, enhancing fire safety on offshore rigs and platforms.
Lightweight:
Compared to metal, engineering plastics offer significant weight reduction. This translates to lighter rigs, platforms, and subsea components, which can improve stability, reduce fuel consumption for transportation and operation, and potentially allow for the use of smaller support vessels.
High Strength and Wear Resistance:
Certain engineering plastics possess excellent strength-to-weight ratios, making them suitable for demanding applications while remaining lightweight. Their wear resistance minimizes friction and maintenance needs in critical components.
These properties translate to several advantages for the offshore industry:
Reduced Maintenance Costs:
Corrosion resistance and wear resistance lead to less downtime and lower maintenance costs for offshore equipment.
Enhanced Safety:
Flame retardant options contribute to a safer working environment on offshore rigs.
Improved Operational Efficiency:
Lighter weight platforms and components can potentially lead to lower fuel consumption and operational costs.
Design Flexibility:
Engineering plastics allow for the creation of lightweight yet strong components with complex shapes, potentially leading to more efficient designs for offshore applications.
In conclusion, engineering plastics are making a significant impact in the offshore industry by enabling lighter, more corrosion-resistant, and potentially more cost-effective equipment, while contributing to improved safety and operational efficiency.
Materials list
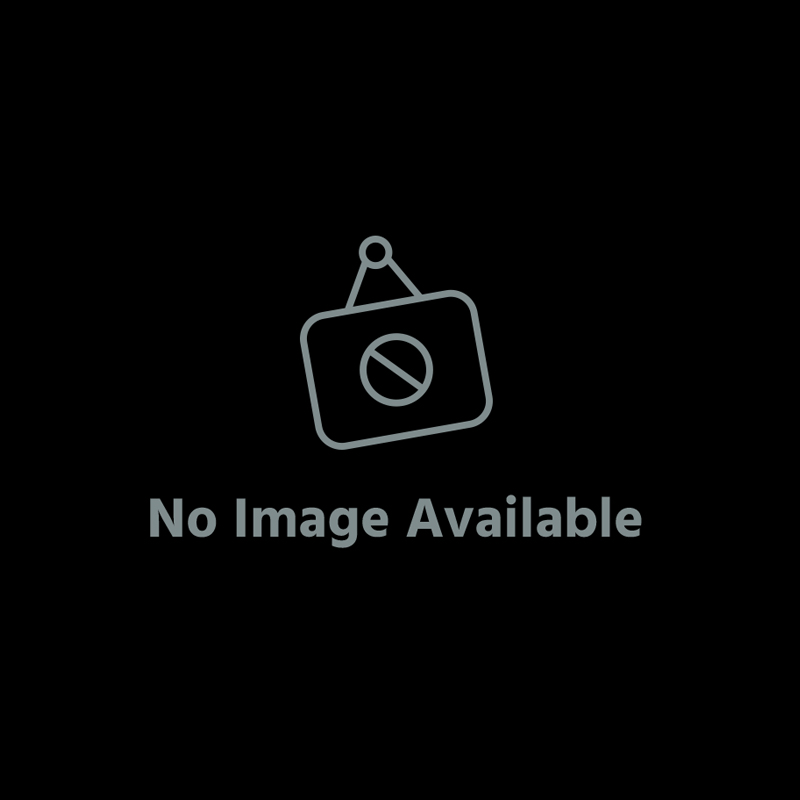
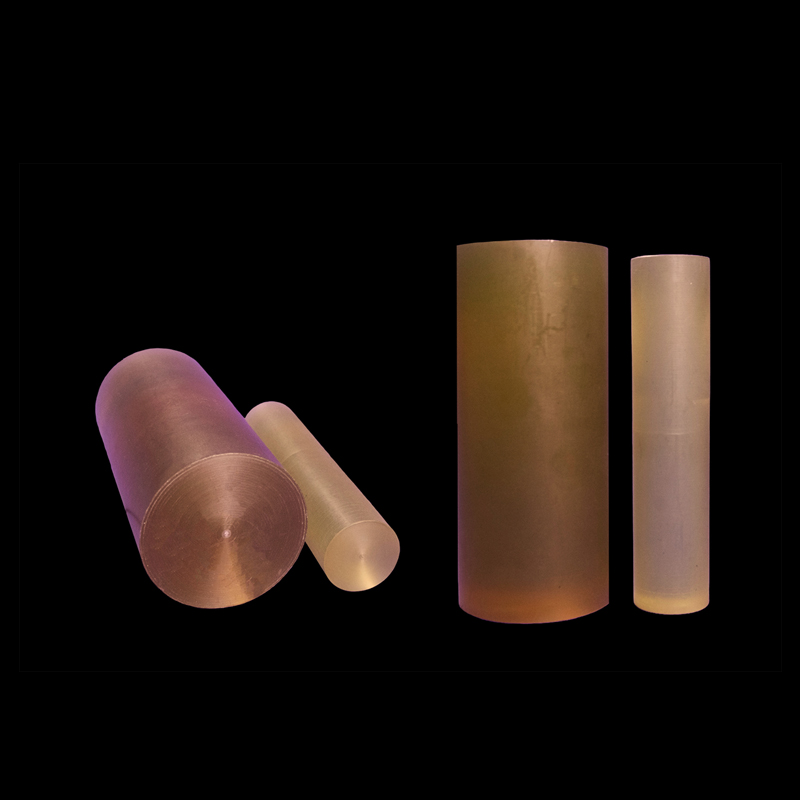
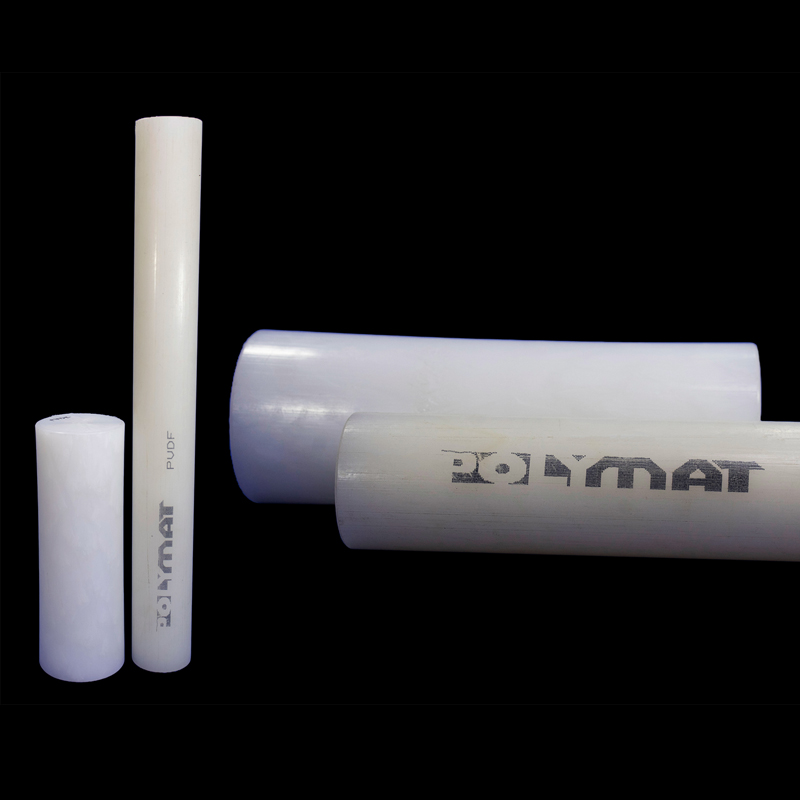