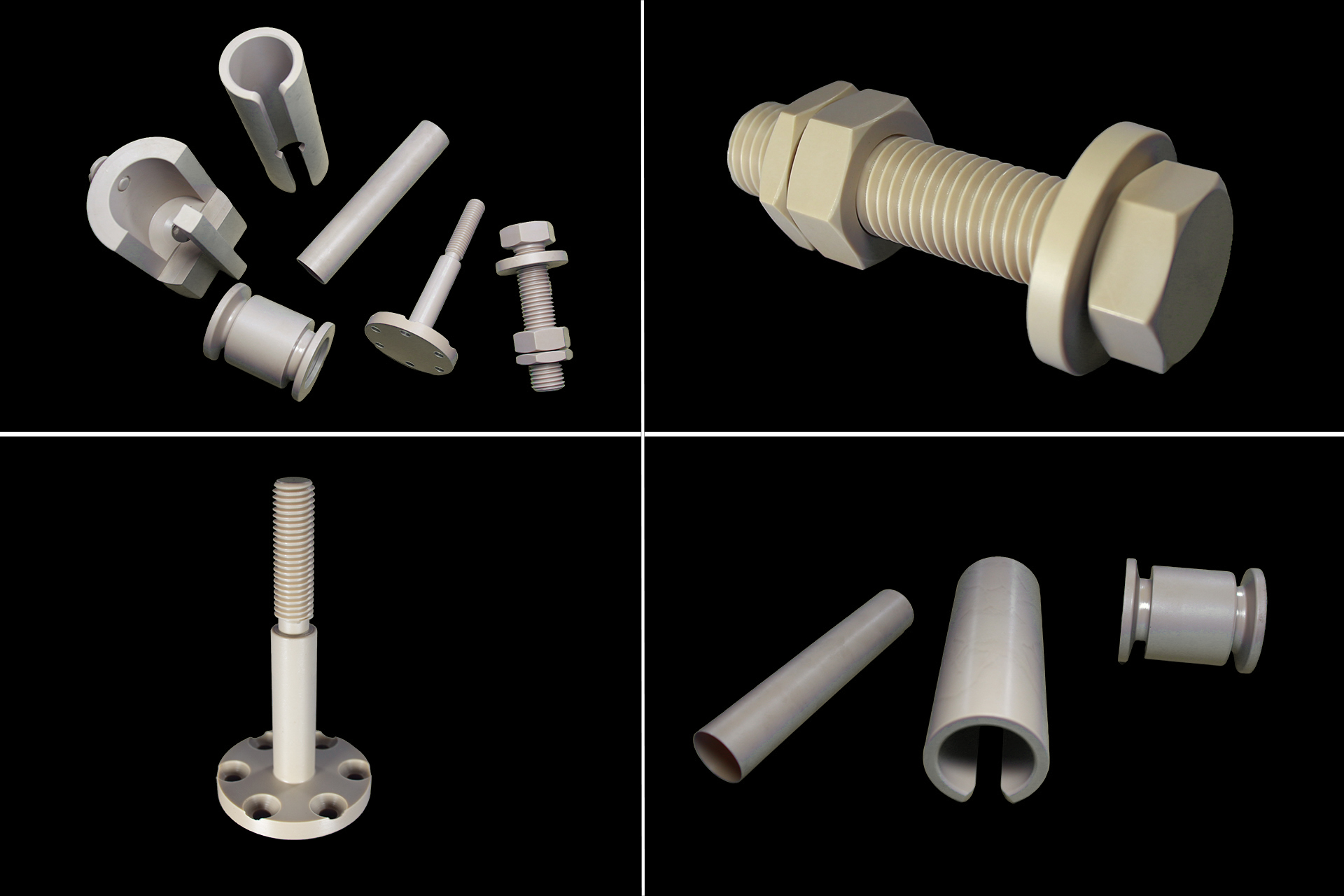
Polymat Peek
Polyether Ether Ketone (PEEK) is a high-performance thermoplastic that stands out in the world of advanced materials due to its exceptional mechanical, thermal, and chemical properties. Whether you’re in aerospace, automotive, medical, or industrial sectors, PEEK delivers unparalleled performance and reliability.
Mechanical Properties
- High Tensile Strength: Up to 90 MPa, providing robust performance under stress.
- Excellent Impact Resistance: Capable of withstanding high-impact forces without significant deformation or failure.
- Superior Fatigue Resistance: Maintains performance and durability over repeated stress cycles, reducing the likelihood of material failure.
- Low Coefficient of Friction: Reduces wear and tear, enhancing the longevity of components such as bearings and gears.
- High Modulus of Elasticity: Ensures rigidity and stability under load, maintaining shape and performance in high-stress applications.
- Outstanding Creep Resistance: Resists deformation under constant load over time, ensuring long-term dimensional stability.
Thermal Properties
- High Continuous Service Temperature: PEEK can maintain its mechanical properties and structural integrity at temperatures up to 250°C (482°F) for extended periods.
- Exceptional Thermal Stability: The material remains stable and does not degrade when exposed to high temperatures, making it suitable for demanding thermal environments.
- Low Thermal Expansion: PEEK exhibits minimal thermal expansion, which ensures that it retains its dimensional accuracy and mechanical properties despite temperature fluctuations.
- High Glass Transition Temperature: PEEK has a glass transition temperature around 143°C (289°F), above which it maintains its mechanical strength and rigidity.
- Thermal Insulation Properties: It provides effective insulation against heat, helping to manage thermal conditions in various applications.
- Thermal Oxidative Stability: PEEK resists oxidation and degradation in high-temperature oxidative environments, ensuring long-term performance and durability.
Chemical Properties
- Exceptional Chemical Resistance: PEEK is highly resistant to a wide range of chemicals, including acids, bases, and organic solvents.
- Resilience to Corrosive Environments: It withstands exposure to harsh chemicals without significant degradation, making it ideal for use in chemical processing and industrial applications.
- Resistance to Hydrolysis: PEEK maintains its mechanical properties and dimensional stability even when exposed to moisture and high-pressure steam, reducing the risk of hydrolytic degradation.
- Non-reactivity: The material does not react with most chemicals, ensuring it remains stable and maintains performance in aggressive environments.
- Durability in High-Temperature Chemical Environments: PEEK retains its chemical resistance even at elevated temperatures, providing reliable performance in extreme conditions.
- Low Permeability: It has low permeability to gases and liquids, which helps in applications requiring containment of fluids or gases.
Application Sectors
1. Aerospace
PEEK is used in aircraft components, turbine blades, heat shields, and structural parts due to its high strength-to-weight ratio, excellent thermal stability, and superior resistance to extreme temperatures and harsh environments.
2. Automotive
PEEK is utilized in engine parts, transmission components, fuel system parts, and bearings, thanks to its high mechanical strength, resistance to high temperatures and automotive fluids, and its low friction and wear properties.
3. Medical
PEEK is employed in spinal implants, surgical instruments, dental prosthetics, and prosthetic devices due to its biocompatibility, resistance to sterilization processes, high mechanical strength, and chemical resistance.
4. Chemical Processing
PEEK is used in applications such as pumps, valves, seals, liners, and reactors because of its excellent chemical resistance to acids, bases, and solvents, high thermal stability, and durability under high pressure and temperature.
5. Oil and Gas
PEEK is utilized in downhole equipment, seals, gaskets, and bushings due to its high resistance to corrosive environments, ability to withstand extreme temperatures and pressures, and exceptional mechanical strength. and durability.
6. Electronics and Electrical
PEEK is used in insulators, connectors, housings, and electronic components because of its high electrical insulating properties, thermal stability, resistance to electrical arcing, and excellent dimensional stability.
7. Industrial Manufacturing
PEEK is utilized in bearings, gears, wear pads, bushings, and seals due to its high wear and abrasion resistance, low friction, durability in high-stress applications, and thermal stability.
8. Defense and Military
PEEK is employed in ballistic armor, precision components, and high-strength structural parts due to its high impact resistance, lightweight nature with a high strength-to-weight ratio, durability in extreme conditions, and resistance to chemicals and temperatures
9. Semiconductors
PEEK is used in wafer handling parts, process equipment components, and semiconductor fabrication tools because of its high thermal stability, low outgassing, precision, and resistance to high temperatures and vacuum environments.
10. Food and Beverage
PEEK is used in Components for processing and packaging machinery, food handling equipment because of its Compliance with food safety standards, resistance to high temperatures and cleaning agents, durability in processing environments.
11. Energy
PEEK is used for renewable energy systems, such as wind turbine parts and solar panel components. Because of its High strength, resistance to environmental conditions, and longevity under operational stresses.
12. Textile and Apparel
PEEK can be used as High-performance fibers and fabrics for specialized clothing and gear. Because of its Strength, durability, and resistance to wear and environmental factors.