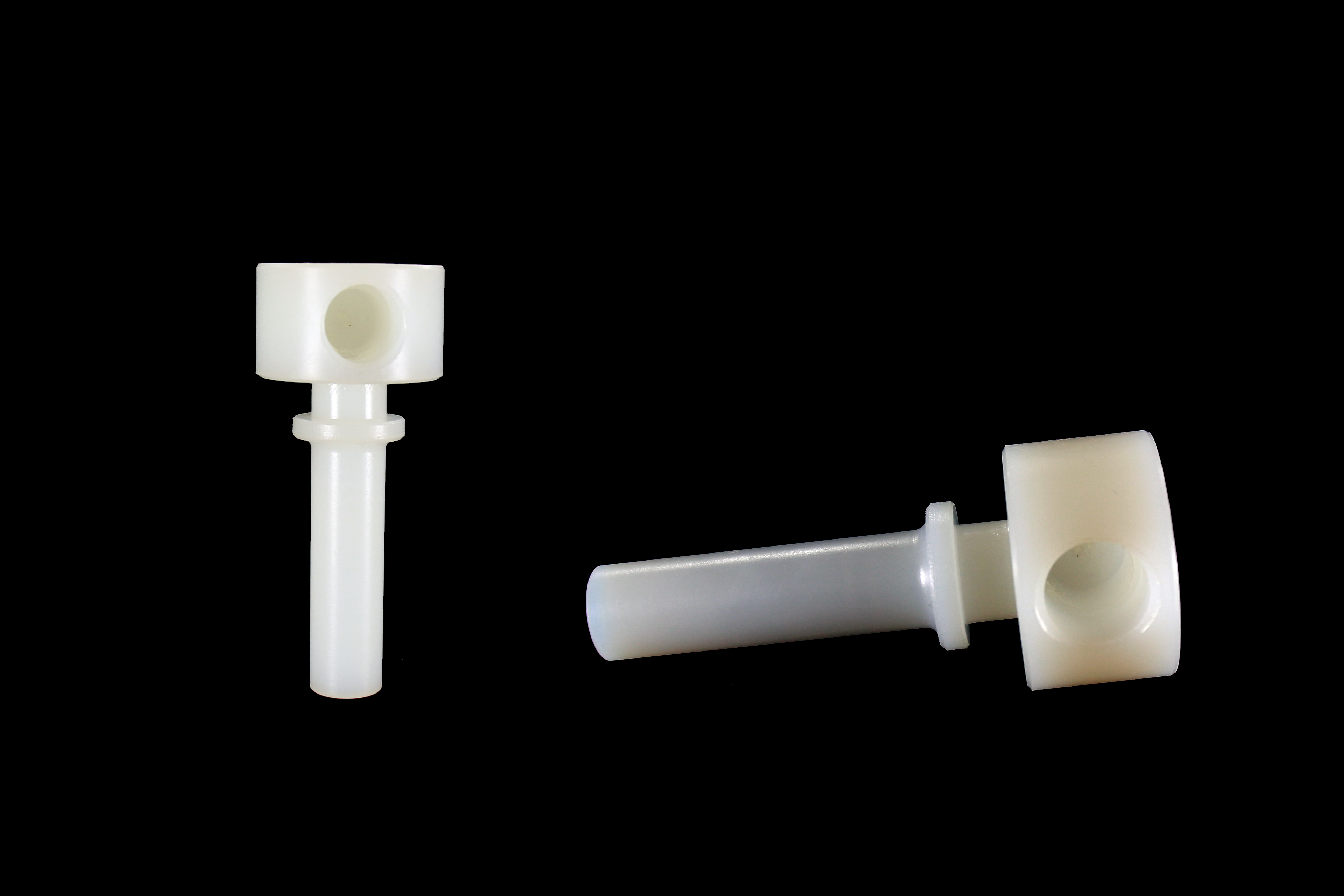
Polymat PTFE
Polytetrafluoroethylene (PTFE), commonly known by the brand name Teflon, is renowned for its chemical resistance and non-stick properties. However, its mechanical strength characteristics are also notable.
Mechanical Properties
- Tensile strength : PTFE typically exhibits a tensile strength of approximately 15 to 30 MPa (megapascals) or 2,200 to 4,350 psi (pounds per square inch). While not as high as some other polymers, PTFE's strength is adequate for many applications.
- Impact Resistance: PTFE has relatively low impact resistance compared to some other engineering plastics. The Izod impact strength is generally low, often less than 5 J/m (joules per meter) or 0.25 ft-lbf/in, indicating that it can be brittle under impact stress.
- Modulus of Elasticity: The modulus of elasticity for PTFE is typically around 500 to 700 MPa (megapascals) or about 70 to 100 ksi (kilopounds per square inch). This relatively low modulus indicates that PTFE is more flexible and less rigid compared to some other engineering plastics.
- Flexural Strength: PTFE shows a flexural strength of approximately 20 to 30 MPa (megapascals) or 2,900 to 4,350 psi. This property indicates its resistance to bending and deformation under load.
- Creep Resistance: PTFE exhibits significant creep under sustained load, especially at elevated temperatures. It tends to deform over time when subjected to continuous stress, which can affect its performance in long-term applications.
- Dimensional Stability: Despite its creep tendencies, PTFE maintains good dimensional stability in various environments, due to its low coefficient of thermal expansion. It does not expand or contract significantly with temperature changes.
- Fatigue Resistance: PTFE's fatigue resistance is moderate. While it can handle some repeated stress cycles, its overall performance may be affected by continuous or high-frequency stress.
Thermal Properties
- Glass Transition Temperature (Tg): PTFE has a low glass transition temperature, typically around -100°C to -110°C (-148°F to -166°F). This means that PTFE remains flexible and functional even at very low temperatures.
- Melting Temperature (Tm): PTFE has a high melting temperature, generally around 327°C (621°F). This high melting point makes PTFE suitable for applications that involve high temperatures.
- Continuous Service Temperature: PTFE can be used continuously at temperatures up to about 260°C (500°F). This range indicates that it maintains its mechanical properties and chemical resistance in high-temperature environments.
- Thermal Decomposition Temperature: PTFE begins to decompose at temperatures above 400°C (752°F). It is stable and maintains its integrity well below this temperature, but exposure to temperatures above this threshold can lead to thermal degradation.
- Thermal Stability: PTFE exhibits excellent thermal stability within its service temperature range. It retains its physical properties and performance even under prolonged exposure to elevated temperatures.
- Thermal Expansion: PTFE has a relatively low coefficient of thermal expansion, which means it undergoes minimal dimensional changes with temperature fluctuations. This contributes to its dimensional stability in varying thermal conditions.
- Thermal Cycling Resistance: PTFE shows good resistance to thermal cycling, meaning it can endure repeated heating and cooling cycles without significant degradation in performance
Chemical Properties
- Acids: PTFE shows excellent resistance to a wide range of acids, including both strong acids (like sulfuric acid and hydrochloric acid) and weak acids. It remains stable and maintains its properties when exposed to acidic environments.
- Bases: PTFE is highly resistant to bases, including strong alkaline solutions such as sodium hydroxide and potassium hydroxide. It does not degrade or lose its integrity when exposed to concentrated alkaline environments.
- Solvents: The material demonstrates exceptional resistance to many organic solvents, including alcohols, esters, ketones, and hydrocarbons. However, PTFE can be affected by highly aggressive solvents like chlorine trifluoride and some fluorinated solvents.
- Oxidizing Agents: PTFE has moderate resistance to oxidizing agents. It can handle exposure to agents like hydrogen peroxide and chlorine, but prolonged or high-concentration exposure can lead to some degradation.
- Hydrolysis: PTFE is resistant to hydrolysis, making it suitable for use in humid environments and applications involving steam or water without significant degradation.
- Fuel and Oils: The material exhibits strong resistance to fuels, lubricating oils, and greases, which makes it suitable for applications in automotive and industrial settings where such substances are common.
- Detergents and Cleaning Agents: PTFE is resistant to many common detergents and cleaning agents, allowing it to withstand frequent cleaning processes without losing its chemical resistance or performance.
- Gas Permeability: PTFE has very low gas permeability, which is advantageous in applications requiring isolation of gases or maintaining a controlled environment.
Application Applications
- Chemical Processing: PTFE is widely used in chemical processing equipment such as gaskets, seals, and lining materials for reactors, pipes, and valves due to its resistance to corrosive chemicals and high temperatures.
- Aerospace: Utilized in aerospace components like seals, bearings, and insulation for wires and cables. PTFE’s thermal stability and low outgassing properties make it suitable for high-performance aerospace applications.
- Electronics: Employed in electronic components such as insulators, connectors, and cables. PTFE’s excellent electrical insulating properties and resistance to high temperatures make it ideal for these applications.
- Medical Devices: Used in medical devices and implants due to its biocompatibility and resistance to sterilization methods. Applications include surgical instruments, catheters, and coatings for medical devices.
- Food Processing: PTFE is used in food processing equipment, including non-stick coatings for cookware, conveyor belts, and liners for food processing machinery. Its non-stick and easy-to-clean properties are highly valued in this industry.
- Pharmaceuticals: Applied in pharmaceutical manufacturing for components like tubing, seals, and valves that require high chemical resistance and purity. PTFE helps maintain the integrity of pharmaceutical products.
- Automotive: PTFE is used in automotive applications such as seals, gaskets, and bearings. Its resistance to fuels, oils, and high temperatures makes it suitable for various automotive components.
- Oil and Gas: Employed in the oil and gas industry for seals, gaskets, and lining materials in equipment that is exposed to harsh chemicals and high pressures. PTFE’s chemical resistance is crucial for these applications.
- Semiconductor Manufacturing: Used in semiconductor fabrication for components such as gas handling systems and vacuum seals. PTFE’s low outgassing and chemical resistance are critical for high-purity environments.
- Construction: Applied in construction for architectural coatings, insulation materials, and seals that require resistance to weathering, UV radiation, and chemicals.